Rewiring America: The Effect of the EV Economy on Labor
- Collin Griffin
- Oct 22, 2019
- 4 min read
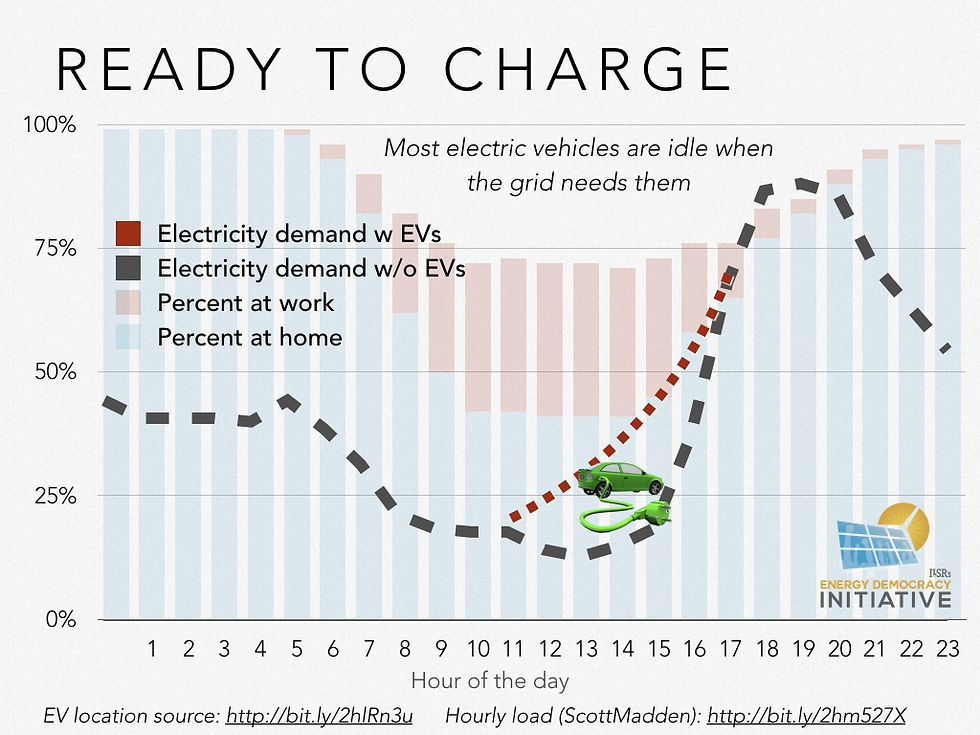
As the UAW strike marches on into its fifth week, the auto industry stands positioned for immense change, almost entirely due to the astronomical growth of electric vehicles (EVs). The industry has been flooded by new vehicle announcements, from high end models like the Porsche Taycan (starting at a whopping $150,900, with the optioned-out, highest trim level topping in at $241,500), to more practical, familiar models like the Volvo XC40 crossover (starting below $50,000), to the new entry from the EV founding fathers, the Tesla Model Y (ranging between $39,000 to $62,000). It’s no secret that the market is expanding rapidly, as even legacy automakers are now conceding and switching some or all of their lineup to hybrid or electric models. The total global EV fleet exceeded 5.1 million vehicles in 2018, up 2 million from 2017, and is on track to continue to grow for the remainder of 2019. EVs clearly define the future of transportation: one with lower costs, far fewer environmental impacts, and with greater safety from automation. However, a looming question mark awaits in the dark recesses of the assembly plants of legacy automakers and vehicular startups alike: what place does labor have?
As the United Autoworkers strike rounds its third week, General Motors is reported to have lost nearly $1 billion in productivity. The UAW has based the strike on a number of reasons, many related to wages, benefits, and layoffs. However, a common thread runs through this picket line, spun by the fears caused by GM’s massive bet on the future of the automobile. GM has announced plans for “Zero Crashes, Zero Emissions, and Zero Congestion,” based on which it will massively overhaul its current fleet, employing technologies like vehicle autonomy, connectivity, and of course, electricity, in order to save lives, the planet, and people’s time. A rosy aspiration, and one that is perhaps not incredibly far fetched, as the exploding EV and self-driving car market has shown. While this moonshot for a better future may still be a few years out, the impact on workers has already crept its way into reality.
The closing of The GM plant in Lordstown, Ohio is perhaps the most obvious indication of the direction of GM’s future plans. The Chevy Cruze, which was built at the plant, was discontinued as a part of GM’s move to update its vehicle lineup and make way for its electric and autonomous vehicles. In March of 2019, the plant was shuttered, laying off 4,500 workers, with GM now attempting to sell off the factory to a smaller EV start-up (which had a total of 99 full-time employees last year). The plant’s closing drew comparisons to the infamous Campbell Works closing by Youngstown Sheet & Tube in 1977 referred to as “Black Monday.” The closing was seen by many as the death knell for Youngstown, Ohio, and it’s obvious why: its population has declined from above 150,000 to below 65,000 and the poverty rate is 35%, more than double the national average. Youngstown’s story is not particularly unique either, hundreds of industrial towns and cities across Rust Belt have suffered a similar fate, with varying levels of recovery. But could the closing of even more factories, especially those in the automotive industry, lead to a “Second Wave” of deindustrialization in one of America’s most vulnerable regions?
The workforce employed by GM and other automakers has already declined massively, even before the introduction of EVs. Today, the total number of auto workers employed by GM totals about 46,000 down from 259,000 in 1991. EV manufacturing will only exacerbate these losses: both Ford and Volkswagen have estimated that EV manufacturing requires 30% less production effort. The mechanical simplicity of EVs also means that the jobs may be even further outsourced, with many of the parts being shipped to the US preassembled, requiring only low-skill or even completely automated final assembly within US plants. The job losses and displacement by low-skilled workers are not easy to make up for, either. Workers at most GM plants make an average of $30 per hour: an annual salary of about $62,000. With many auto workers lacking higher education, their specialized skill sets may be worth next to nothing (or as the Federal government calls it, $7.25 an hour) in the clean, green, lean economy of tomorrow.
It would be remiss to suggest that the inevitable labor issues that will arise with the move to automation and EVs call for the halting of progress and the continued proliferation of our current petroleum-powered, pollution-palooza. It is clear that quality of life will improve across the board, and the move to more sustainable modes of transit are crucial to combating climate change. But as eager as we are to embrace an electric and autonomous trip into the future, we must also be steadfast in ensuring that the path forward is just as clear for the individuals who built the cars, trucks, planes, and trains that got us to our first stop.
Sources:
Yorumlar